What is Corrugated Cardboard?
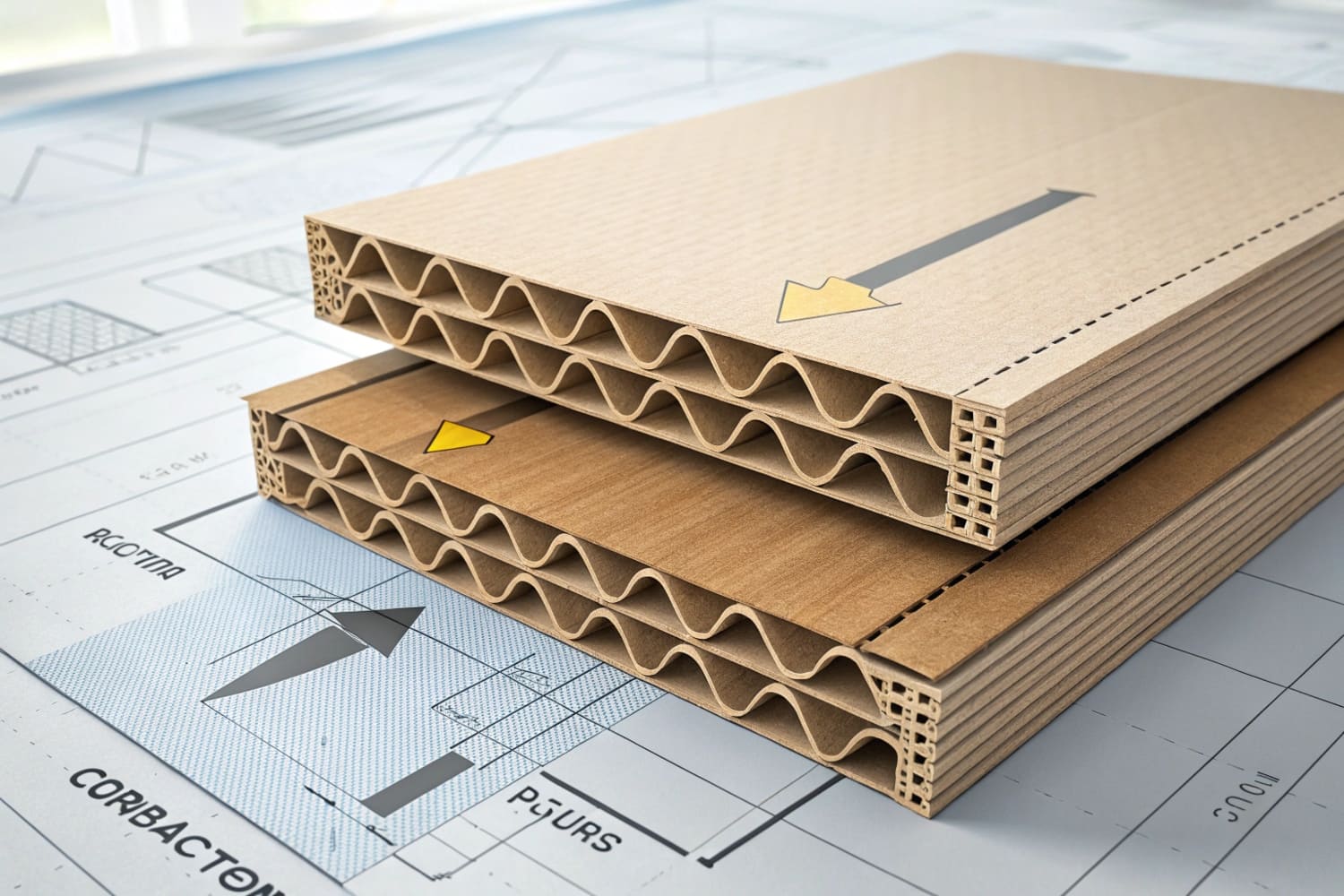
I once opened a new flat-packed display and saw the box was crushed at one corner—inside, my products survived. That small shock started my deep dive into corrugated cardboard.
Corrugated cardboard is a paper-based material made from one or more fluted inner layers glued between flat linerboards, creating a light yet remarkably strong sandwich used for shipping and retail displays.
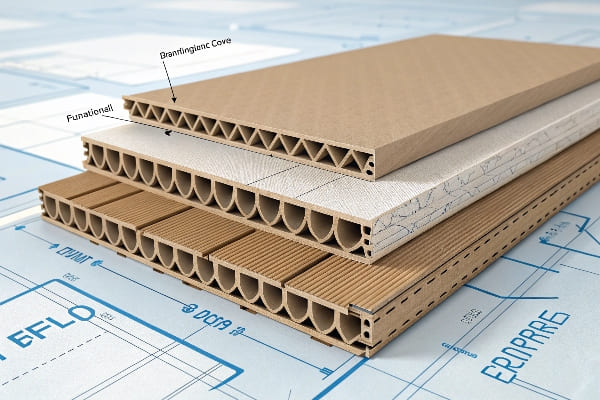
That quick answer is helpful, but strength, cost, and sustainability hide richer stories. Keep reading and decide if corrugated board is the hero your goods deserve.
What is the difference between corrugated cardboard and regular cardboard?
At first glance, two brown boards look the same; the wrong choice costs money and trust.
Corrugated cardboard has air-filled flutes between liners, while regular cardboard (chipboard) is a single solid layer, so corrugated is stiffer, tougher, and lighter.
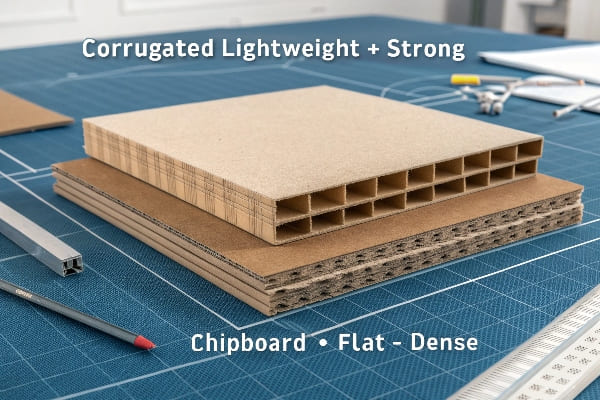
Structure, Performance, and Cost
I design displays daily, and the choice between corrugated and regular board shapes price, strength, and image.
1. Anatomy
Property | Corrugated1 | Regular (Chipboard2) |
---|---|---|
Layers | Liner–Flute–Liner | One solid sheet |
Typical Thickness | 2 mm–7 mm | 0.3 mm–1 mm |
Weight per m² | Low to medium | Low |
2. Performance
- Compression: Flutes act like tiny arches. They spread load. A 5 kg crossbow on a B-flute stand shows no sag for months. Chipboard would bow in a week.
- Shock Absorption: Air pockets cushion drops. My US buyer David once sent back sample photos: outer corners crushed, inner crossbows untouched.
- Print Quality: Chipboard’s smooth face prints like a magazine cover, perfect for folding cartons. Corrugated needs high-quality liners or lamination to match but holds shape better on retail floors.
3. Cost and Sustainability
Corrugated uses more fiber but saves freight through lower breakage and lighter weight. Both boards can be recycled, yet corrugated often contains higher post-consumer content. When I ship thirty displays per pallet to California, corrugated saves one full pallet in damage returns each quarter, balancing its slightly higher unit price.
Corrugated’s layered core remains the winning choice for large, stand-up displays because it solves breakage pain without blowing budgets.
What counts as corrugated cardboard?
Seeing “corrugated” on a spec sheet can confuse a first-time buyer who meets dozens of board codes and flute names.
Any paperboard that sandwiches a wavy fluted medium between at least one flat liner qualifies as corrugated cardboard, regardless of flute size, liner coating, or wall count.
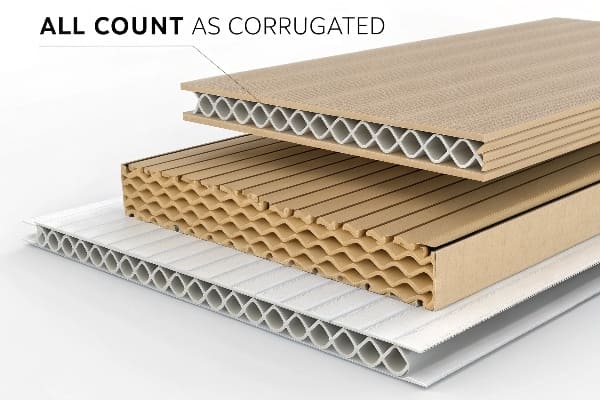
Flute Profiles3, Wall Types, and Coatings
When I walk a new client through my factory, I always pull sample cuts from the line. Knowing profiles prevents ordering the wrong board.
1. Flute Profiles
Code | Height (mm) | Flutes per 30 cm | Common Use |
---|---|---|---|
A | 4.8 | 33 | Appliance cartons |
B | 2.6 | 47 | Retail boxes, POP stands |
C | 3.6 | 38 | Shipping cartons |
E | 1.6 | 90 | High-graphic packaging |
F | 0.8 | 125 | Cosmetic sleeves |
Tall flutes insulate and resist crush; short flutes fold neatly for graphics.
2. Single, Double, Triple Wall4
- Single Wall: One flute. Light, economical.
- Double Wall: Two different flutes laminated. My crossbow floor displays use BC double wall: C absorbs shock, B adds stacking strength.
- Triple Wall: Three flutes. Acts like plywood for export crates.
3. Coatings and Liners
Kraft liners give a wood-like look; white-top liners invite vivid print. Water-resistant coatings let me supply fishing-gear brands that store displays in damp shops.
If your sheet has at least one flute, it counts as corrugated, even when laminated with foil, PET, or cotton paper.
What is an example of a corrugated cardboard?
Theory feels distant until you picture a real product on a shelf.
A typical double-wall BC-flute display stand that holds hunting crossbows in sporting-goods stores is a prime example of corrugated cardboard in action.
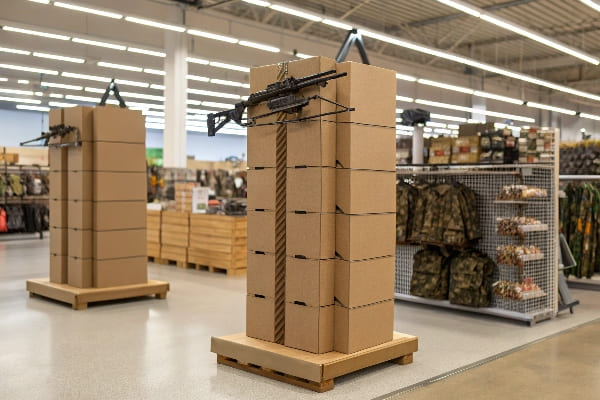
Case Study: Popdisplay’s Crossbow Tower
I built this unit last spring for David at Barnett Outdoors.
1. Design Goals
Goal | Requirement | Solution |
---|---|---|
Load | Hold 40 kg total | BC-flute core, H-shaped inserts |
Brand Impact | Full bleed graphics | White-top liner + offset print |
Speed | 20-day delivery | In-house die-cut + UV drying |
2. Prototype to Mass Production
We shared 3D renderings within 24 hours. Two physical samples shipped to Dallas. After drop testing at his lab, only a corner guard needed a tweak. Because corrugated5 cuts clean and folds flat, I sent the final batch in knock-down kits; local staff assembled displays on site without tools.
3. Results
- Sales Lift: Retail partner reported a 25 % sales bump6 over peg-wall presentation.
- Durability: Units stayed rigid for a three-month promo even with customers pulling bows out daily.
- Reorders: David doubled his next order and asked for a matching countertop version, again in corrugated.
This example shows how corrugated’s mix of strength, lightweight, and printability supports demanding retail goals at scale.
How do I know if a box is corrugated?
Standing in a warehouse, you need a quick test before boxes load onto the truck.
Slice an edge and look for a wavy layer between two flat sheets; the visible flute confirms the box is corrugated cardboard.
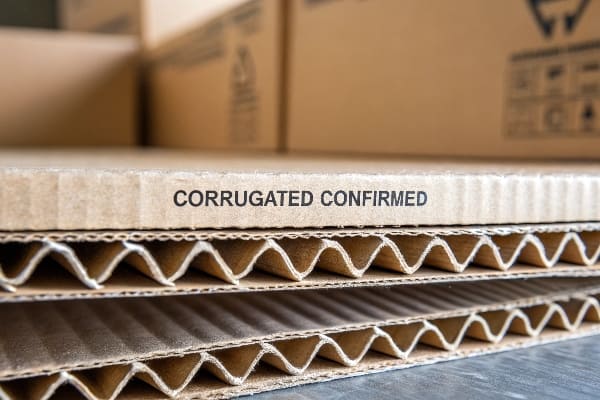
Five Quick Identification Methods
Over years inspecting supplier lots, I use these simple checks.
1. Visual Edge Cut
Open a seam with a knife. Flutes jump out as zig-zag arches. Chipboard will appear solid.
2. Finger Tap Sound
Tap the panel. Corrugated gives a hollow drum sound because of air pockets. Chipboard sounds dead and solid.
3. Weight-to-Size Ratio7
A large corrugated box feels lighter than its volume suggests. Chipboard grows heavy fast.
4. Compression Test8
Press the broad face with your palm. Corrugated springs back gently; chipboard creases before spring.
5. Manufacturer Codes
Look for stamps: “B-Flute 32 ECT” or “200 # Test.” These ratings belong only to corrugated board.
Method | Tools Needed | Time (sec) |
---|---|---|
Edge Cut | Knife | 10 |
Sound | None | 2 |
Weight | Scale (optional) | 5 |
Palm Press | None | 3 |
Code Check | Eyes | 5 |
Use at least two methods to avoid mix-ups. I once saved a client from shipping heavy telescopes in single-layer chipboard by spotting the wrong edge pattern during final QC—preventing thousands in damage claims.
Conclusion
Corrugated cardboard hides simple strength in its arches; know its traits and you protect products, budgets, and reputations with one smart material choice.
Explore the advantages of corrugated board, including strength and cost-effectiveness, to enhance your display designs. ↩
Learn about chipboard’s print quality and applications to make informed choices for your display projects. ↩
Understanding Flute Profiles is essential for selecting the right packaging for your products, ensuring safety and presentation. ↩
Exploring the differences in wall types helps in choosing the best packaging solution for durability and cost-effectiveness. ↩
Explore how corrugated materials enhance retail displays with their strength and lightweight properties, making them ideal for various applications. ↩
Discover strategies and case studies on how effective retail displays can lead to significant sales increases, like the reported 25% sales bump. ↩
Understanding the weight-to-size ratio can help you choose the right packaging, ensuring cost-effectiveness and efficiency. ↩
Learning how to conduct a compression test can enhance your quality control processes, ensuring your products are well-protected during shipping. ↩