What About the Disadvantages of Corrugated Boxes?
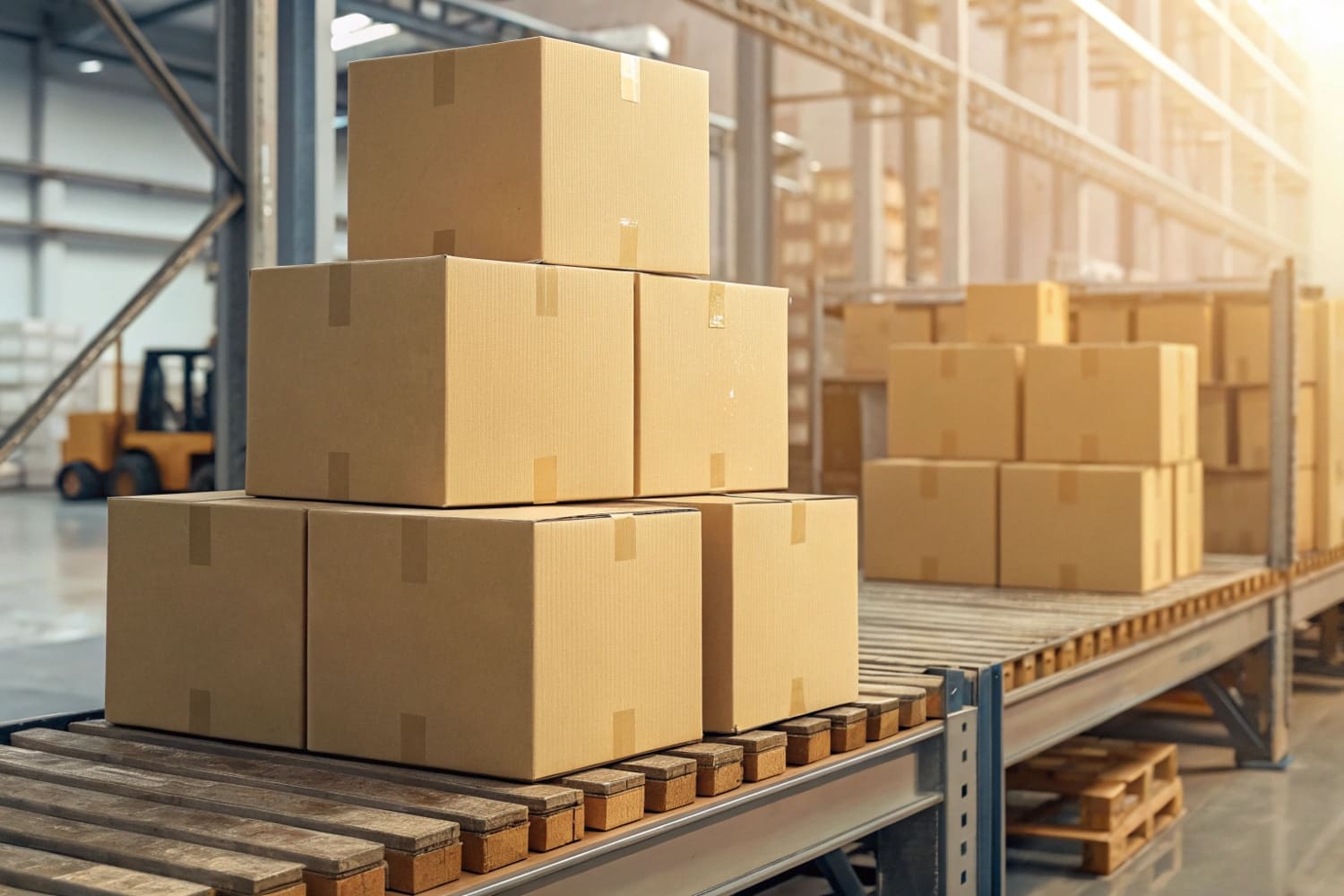
You trust corrugated boxes to guard your products, yet hidden flaws can erode profits. I expose these weak points and show safer paths.
Corrugated boxes suffer from moisture sensitivity, limited weight capacity, space inefficiency before use, and inconsistent recycling routes; choosing treated board, better stacking plans, and verified recyclers reduces these drawbacks.
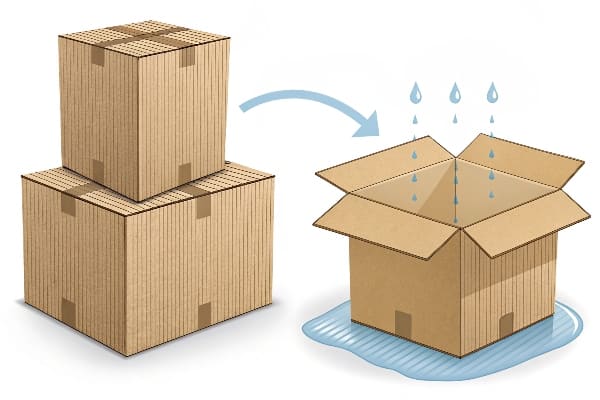
Stay with me as I unpack each drawback in plain language, share factory-floor observations, and outline steps that keep my own export displays arriving sound and sharp.
What are the disadvantages of corrugated boxes?
Broken corners during rain season cost me a full container of returns once; that pain still stings, and it drives this honest list of risks.
Corrugated boxes are weak against water, dent under high point loads, take up room before packing, and can hide inconsistent paper quality that hurts stacking strength.
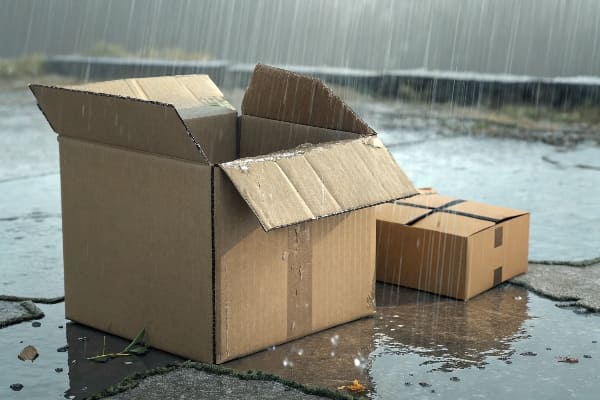
1. Moisture Soaks Strength1
I have watched humidity peel layers apart within hours in Guangdong’s summer. When water breaks the starch glue, compression strength drops by over 30 %, leaving displays sagging on arrival.
2. Point Load Denting
Crossbow limbs poke sharp edges. A single narrow contact point crushes the flute and makes a ripple that travels through the stack, toppling the tower in transit.
3. Space and Handling Cost
Flat blanks still need pallets, and an empty pallet costs the same freight as a full one. Warehouses pay rent on air until the moment of packing.
4. Quality Variance2
Paper suppliers swap grammage without notice. I once opened a shipment that looked fine yet weighed 8 % less. Two weeks later a client sent photos of leaning floor stands.
Drawback | Root Cause | Simple Fix on My Line |
---|---|---|
Water absorption | Untreated paper, open flute | PE-coated liner, shrink wrap |
Point load denting | Low burst rating, thin walls | Double-wall board at stress spots |
Space inefficiency | Flat blanks occupy volume | Produce just-in-time |
Quality variance | Unstable supplier processes | Random weight checks every roll |
I learned these fixes the hard way, but they now sit inside every purchase order I send to the mill. Trust grows when failures fall.
What are the disadvantages of corrugation?
A wavy medium looks simple, yet that wave can betray you when design, tooling, or timing is off.
The corrugation process can introduce flute crush, glue gaps, and high energy use; each flaw lowers strength, wastes material, and inflates cost.
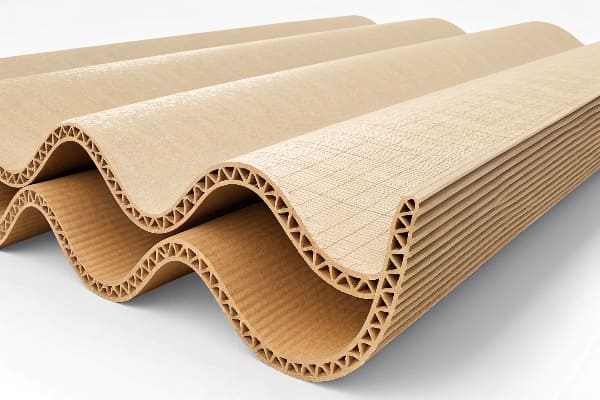
Flute Crush at High Speed
I run three lines at different speeds. When speed exceeds 180 m/min, pressure rollers flatten peaks, reducing thickness by 0.3 mm and cutting stacking strength. Slowing seems costly, yet returns hurt more.
Glue Skips and Delamination
Low-viscosity glue sprays leave small bald patches. Under load these patches shear first, creating the zipper-style failures you see on damaged cartons. Inline infrared glue meters3 reduce this by 70 %.
Energy and Emissions
Steam to heat the medium burns gas. A 2-ply sheet needs about 180 kWh per metric ton. Installing condensate recovery dropped my plant’s fuel use by 12 %, but many vendors still vent heat to the sky.
Process Issue | Impact on Box Life | Factory Control Step |
---|---|---|
Flute crush4 | Low compression strength | Monitor caliper, adjust speed |
Glue skip | Layer separation | Add infrared glue scanner |
High energy demand | Larger carbon footprint | Recycle steam condensate |
I teach buyers to ask for caliper logs and boiler efficiency charts. Clear data forces suppliers to improve instead of excuse.
How long do corrugated boxes last?
Clients often ask if displays can survive a six-month retail campaign. The answer lives in temperature swings and daily foot traffic.
In dry indoor stores, a double-wall corrugated display lasts six months or more, but humidity, UV light, and repeated handling can shorten life to a few weeks.
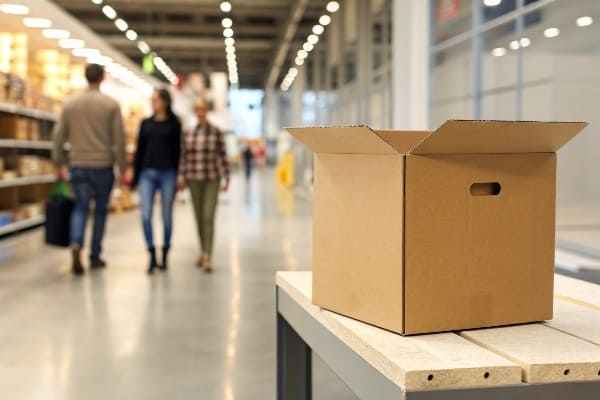
Indoor Versus Outdoor Life
Inside a climate-controlled mall, the board stays near 50 % relative humidity, keeping strength near lab values. Outdoors, morning dew cycles swell and shrink fibers, opening micro-cracks along the flute tips.
Load Fatigue Over Time
Repeated restocking of heavy crossbow bolts adds cyclic stress5. After 1 000 load cycles, edge crush tests show up to 15 % loss. I design internal braces that slide out of sight but share the burden.
UV and Print Fade
Bright point-of-sale lights fade inks. A faded logo undercuts branding faster than a dented corner. I switch to UV-cured inks6 with 7 on the blue wool scale; the extra cost pays back in shelf appeal.
Environment | Expected Life | My Common Countermeasure |
---|---|---|
Dry indoor store | 6–9 months | Standard double-wall |
Humid warehouse | 2–4 months | Wax-coated or laminated liner |
Outdoor promotion | 2–6 weeks | Replace with plastic display |
Knowing these numbers lets buyers schedule refresh stock before failures happen.
Is corrugated cardboard bad for the environment?
Many buyers view paper as “green” by default, yet reality carries more shades of grey.
Corrugated cardboard is renewable and widely recycled, but virgin fiber demand, water use, and transport emissions still impose an environmental cost that only closed-loop programs can cut.
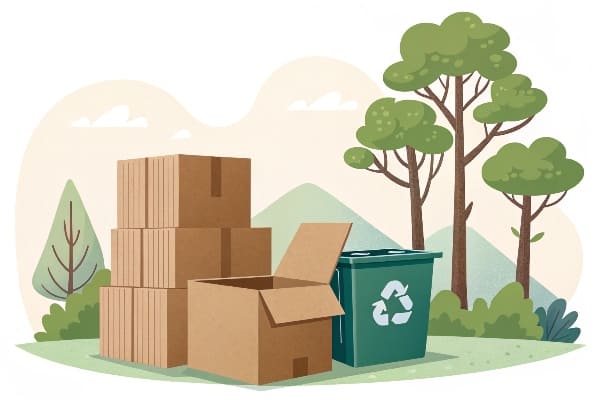
Fiber Source Matters
Virgin kraft comes from managed pine forests, but land-use change can still release carbon. My plant now blends 35 % post-consumer fiber7 without hurting strength, easing pressure on forests.
Water and Chemical Use
Pulping drinks thousands of liters per ton and adds bleaching agents. Closed-loop water systems reclaim up to 85 % of that water and cut effluent loads by half; I chose a mill that invested in this loop.
Transport Footprint
A truck full of flat blanks rides better than one full of air-filled cartons, yet long ocean routes still burn fuel. Grouping orders for clients like Barnett Outdoors into consolidated containers lowers emissions and freight cost by 10 %.
Environmental Concern | Typical Impact | Practical Mitigation |
---|---|---|
Virgin fiber demand | Deforestation pressure | Increase recycled content |
Water consumption | River depletion | Closed-loop water treatment |
Transport emissions | CO₂ from fuel | Consolidated shipping lanes |
Recycling programs work best when boxes stay clean. I print simple “reuse me” icons and run customer webinars on breakdown methods; small steps turn boxes from waste into resource.
Conclusion
Corrugated boxes are not perfect, yet clear knowledge, smart design, and firm supplier checks turn their weak points into manageable costs. I use these steps every day, and failures now stay rare.
Understanding moisture’s impact on material strength can help prevent costly damages and improve product durability. ↩
Exploring strategies to manage quality variance can enhance product consistency and customer satisfaction. ↩
Discover how infrared glue meters can significantly enhance glue application, reducing defects and improving product durability. ↩
Understanding flute crush is crucial for maintaining box strength and quality. Explore this link to learn more about its impact. ↩
Learn about cyclic stress and its impact on material performance, crucial for understanding load fatigue. ↩
Explore this link to understand how UV-cured inks enhance print durability and branding effectiveness. ↩
Explore how post-consumer fiber can enhance sustainability and reduce environmental impact in production. ↩